Sikaflex®-296
Direct glazing adhesive for glass windows in the ship building industry
Sikaflex®-296 is a high performance, elastic, gap-filling, 1-C polyurethane direct glazing adhesive that cures on exposure to atmospheric moisture. It is suitable for almost all kinds of mineral glazing application in the ship building industry.
Sikaflex®-296 meets the regulations set out by the International Maritime Organization (IMO).
- Resistant to ageing and weathering
- Excellent working characteristics
- Solvent- and PVC-free
- Low odour
- Suitable for manual and pump applications
- Black primerless application possible
- Wheelmark approved
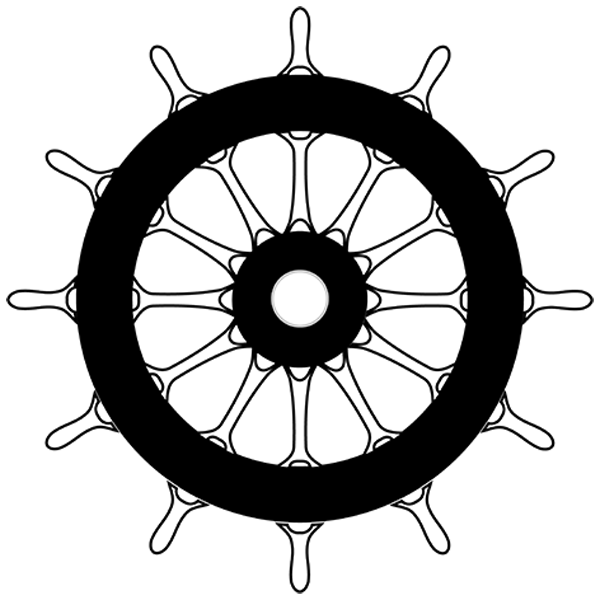